Research & Development
Currently, the on-campus Metal Casting Center is undergoing renovations with state-of-the-art technologies which will make it the most advanced foundry lab in the world.
New technology that is being installed at the MCC include:
- A fully automated green sand molding system
- Including a Simpson batch muller integrated with a Sinto molding machine capable of producing 16” x 20” test molds
- A CB-16 cold box system
- This will allow the MCC to produce large test cores for material characterization projects
- An ARMIL CFS gas furnace
- Preheat investment casting shells.
These new capabilities complement the MCC’s melting equipment, capable of producing heats up to 300 lbs of ferrous and copper-base alloys along with 80 lbs of aluminum.
MCC Resources
The Metal Casting Center has full analytical capabilities including mechanical, chemical and physical testing of materials used in metal casting technology. This includes full green sand and chemical sand testing capabilities and also includes Thermogravimetric Analysis (TGA), Differential Scanning Calorimetry (DSC), High Temperature Dilatometry for Coefficient of Thermal Expansion (CTE), X-ray Fluorescence (XRF), and Particle Size Analysis (PSA).
The center is capable of pouring up to 300 lbs of ferrous or copper base metal and 100 lbs of aluminum in green sand or chemically bonded molds.
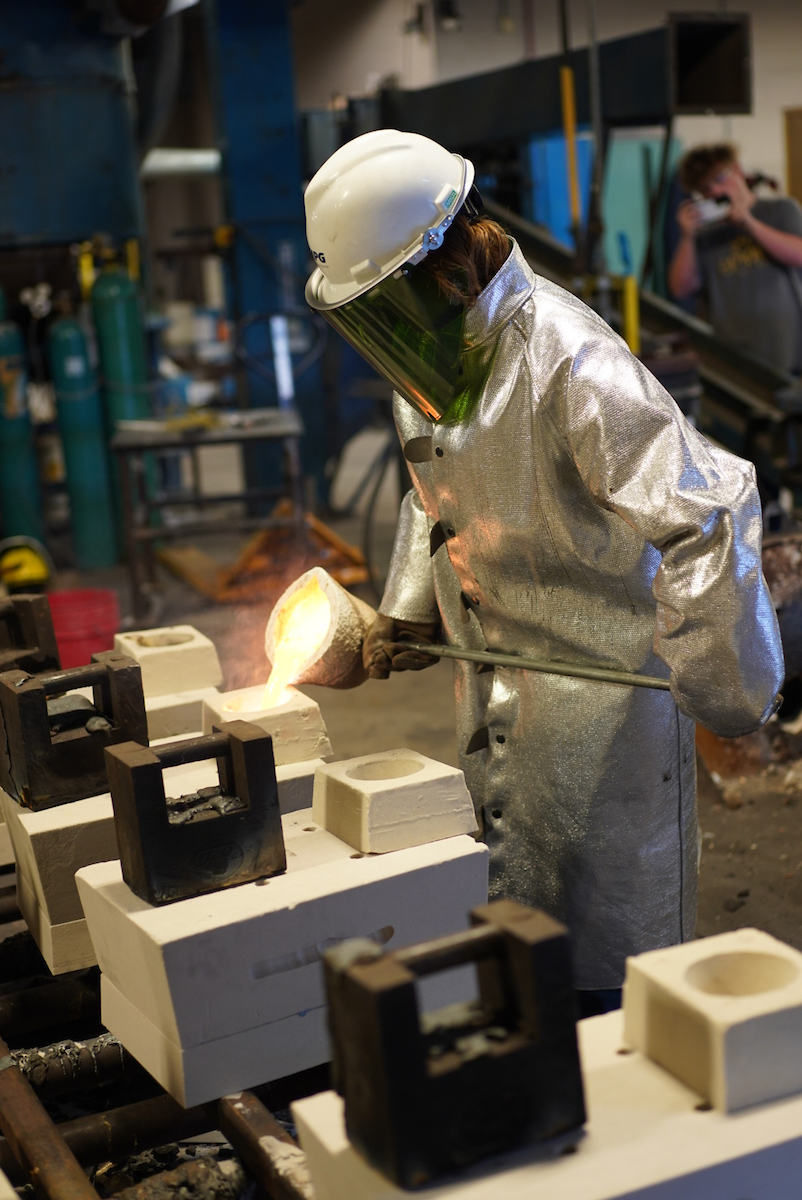
MCC Integration with Foundry 4.0
The foundry is set up for industry 4.0 with all control systems connected to our secure subnetwork. This subnetwork facilitates MQTT protocol which transfers data from controls systems to a centralized database. Data dashboards are developed to create a digital version of the MCC that is representative of the actual facility, advancing towards a digital twin of foundry processes.
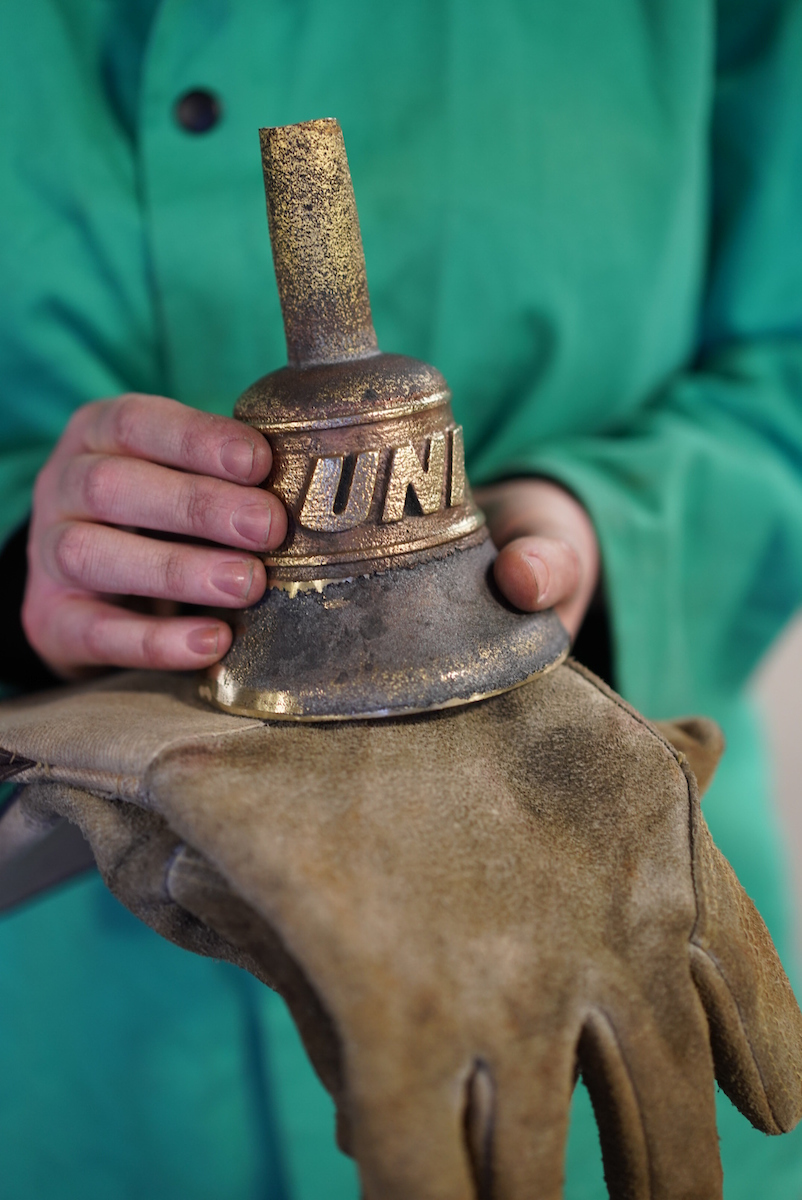